Blacksmithing Shop Tools
Used by Delnero Furniture, Fort Plain, New York


The 50 lb. Little Giant Power Hammer
This hammer was manufactured in 1925 by the Little Giant Manufacturing Company. It was originally purchased by The H.B. Smith Foundry Company of Westfield, Massachusetts. It weighs 1800 lbs. and can forge iron up to 3 inches square. It originally sold for $340.00.Power hammers have been used to help forge metal ever since the smith decided that he needed more capacity to forge a larger mass than he was capable of doing with his own hand. This need generated the idea of using an assistant as a striker, multiple strikers, and then the power hammer.

It doesn't take long to get used to using the power hammer. A job that could take 10 minutes swinging a 4 lb. hammer can be forged in seconds.

The Blacksmith's Treadle Hammer
This treadle hammer was built from the plans designed by Clay Spencer of Madison, Alabama. It has a 65 lb. hammer connected by a adjustable link to the treadle. Three large springs suspend the hammer. Its anvil is made of a 36" X 6" X 6" piece of steel. There are hardie holes in both the hammer and the anvil to hold many different kinds of tools. The treadle hammer has many uses to a smith as many operations require three hands.
Unfortunately, wrought iron has not been produced since around 1911. It has been replaced by mild steel, which is iron with a small amount of carbon in it. For structural work and general machining, this is a better material. It is not however, as satisfactory for blacksmithing. It forges harder than wrought iron and is much more difficult to fire weld. Because it is possible to reuse the same iron many times, today's smiths might find it worthwhile to collect discarded iron for further use.

The Blacksmith's Leg Vise
Most of the blacksmiths' work is done with hand tools. The most commonly used tool is the hammer. There is very little that a smith does that doesn't involve a hammer blow, either directly onto the metal or against a tool over it. Depending on the job the ball peen, cross peen, straight peen and sledge hammers may be used.
Hardies are tools of different shapes which fit into the hardy hole or square hole in the anvil. The most common hardie is called a cutoff hardie and is wedge shaped. It is used to cut metal by placing a hot piece of iron over it and hitting the metal with a hammer, forcing the hardie through the iron.

The vise a blacksmith uses is called a leg vise. It is made differently than a modern engineers' vise. It's made of iron to withstand heavy hammering.
Unlike an engineers' vice, the leg vise is designed to protect the screw treads from the blows.
The smith uses the vise for many jobs including bending work at a 90 degree angle, putting in twists, and any time he needs another hand.

The Forge and Anvil
Blacksmithing is simply hammering hot iron into a desired shape. A way of heating iron and something to hammer it on is all the basic required equipment needed. Early smiths would heat their iron in a wood fire. They soon learned that wood converted to charcoal produced a better fire. By blasting a flow of air into a fire, they were able to produce a much hotter fire.A forge is basically a container for the fire with air inlet for an air blast, connected by a pipe to some sort of bellows or blower. My forge, a Buffalo forge, came out of the H.B. Smith Company of Westfield, Mass.. It's base is laid up block and has a solid steel bottom which supports the Buffalo Tyre. It has an electric blower for the blast and also an exhaust fan in the hood. On the right side there is a four foot by one foot water trough for

Once the smith has heated the iron, he needs a significant support underneath to take the blows. The anvils' solid mass on a good foundation maximizes the smiths effort. A swedge block works the same way, but also offers the smith a variety of contours to help him shape the iron.
Open Daily 10:00 AM to 5:00 PM
Closed Sundays
Evenings by Appointment
Closed Sundays
Evenings by Appointment
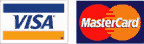